The Vertek™ System
Concrete Structures
Concrete Structures Depend on 2 Sets of Performance Criteria:
1. The structural reinforcements (rebar) and 2. The concrete itself
Both system components graded by strength & flexibility under stress
SeaMix® Admix Grades + Reinforcement Material Choices Create Customizable Value-Add Options For Any User
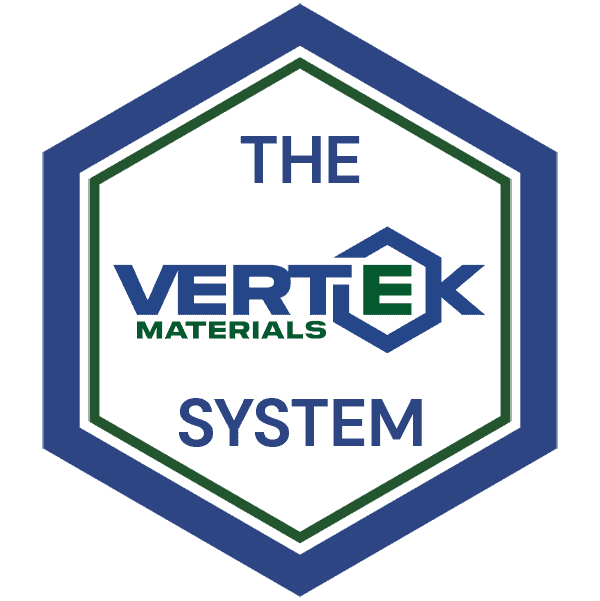
Includes:

Tailored for Strength Enhancement

2x, 5x, & 10x denote levels of
improvement in compressive strength
SeaMix® Benefits:

C:S:A Ratios
Potable/Non potable
Water used
Aggregate Types
Other Additives
SeaMix® Benefits:

Metalic
__Various steels
Non-Metalic
__w Basalt (BFRP)
__ w Glass (GFRP)
BFRP Benefits:

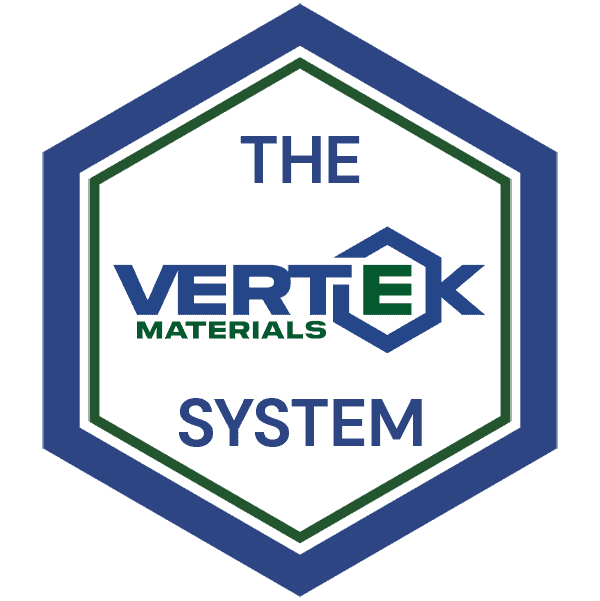
System Benefits:
Vertek™ System Continues To Add Value After Construction
By Slashing Maintenance Needed

By Eliminating Primary Point of Catastrophic Failure


Failure point for structures is nearly always steel reinforcement corrosion
Concrete Admixes
The breadth, versatility, and value of our portfolio of customizable SeaMix® admixes are illustrated by the following three examples:
Example 1: SeaMix® Added to M25 Standard Mix
Demonstrates user ability to tune value set to specific project needs.

Maximized Compressive Strength Case
Std. Strength, Low Cost & Low CO2
Uniform Advantages Across Spectrum
All Value Set Choices Put $ On Bottom Line

Bases
• SeaMix® Admix replaces plasticizers and enables non-potable water use
• Removing 90% of Cement lowers overall carbon footprint by ~80%
• Additional value and carbon reductions from short cycle times, and lower overall concrete use via value engineering not counted
• Carbon Credit value not included
Example #2: SeaMix® in Supermix® Shotcrete
Demonstrates upgrades in strength & cycle time

Notes
• Base Mix: Supermix® ShotCrete 40SHT 1:3:1
• SeaMix® Ultra 2X replaced base admixes•
• All data from Wingerter Laboratories Inc., Miami
• Cost: -5% FOB plant
• Performance: +55%
• Time to spec: -12 days
Example #3: SeaMix® in UHPC Custom Mixes
Demonstrates dramatic reductions in cost and Portland
Typical UHPC vs. SeaMix® Enhanced UHPC

BioCene® in SeaMix® UHPC Mixes:
• Adds compressive strength
• Enables 40% less Portland use
• Slashes cost by at least half
Typical UHPC Values
• Compressive Strength Spec is 17,500 psi
• Cost ranges up to $3000/yd., with typical value of $1300/yd.
• Portland in mix is 30%
SeaMix® UHPC typical results:
• Meets or exceeds 17,500 psi (some values > 22,000 psi)
• Cost ~$600/Yd.
• Portland in mix is ~18%
Vertek™ BFRP Eliminates The Need To Make Trade-Offs and Overcomes GFRP Disadvantages with BioCene®

Design of First FRP Reinforced Concrete Bridge in Florida
(Halls River Project) was Unveiled at the Design Training Expo in 2015
*Design of First FRP Reinforced Bridge in Florida, Masse’us et.al. (FDOT), June 18, 2015

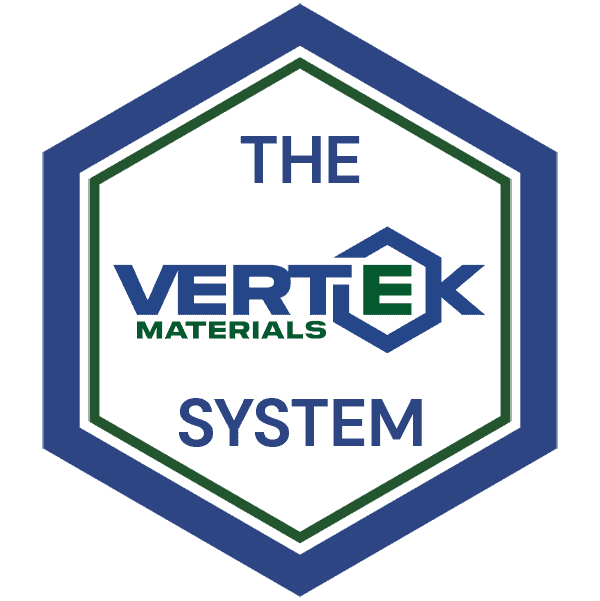
Delivers All Gain & No Pain
BFRP Structural Reinforcements.

BFRP Reinforcement Benefits
Designed to be stronger, lighter, longer lasting than steel, and resistant to salt and chloride, the volcanic-mined basalt rebar materials are a paradigm shift in the construction industry. Hoop and Stirrup pieces also bring similar advantages to weather-exposed uses such as pipe hangers. Shapes can be customized for each use.